Semi-automatic can seamers offer significant advantages in terms of time savings and cost reduction.
Firstly, they increase productivity by speeding up the seaming process. Compared to manual seaming, semi-automatic machines can seal cans at a much faster rate. This means more cans can be processed in a shorter period, reducing overall production time.
The consistency and accuracy of semi-automatic seaming also contribute to time savings. With precise seaming every time, there’s less need for rework or quality checks, minimizing the time spent on correcting errors.
In terms of cost reduction, these machines require less initial investment than fully automated counterparts. This makes them a more affordable option for businesses, especially those with limited budgets.
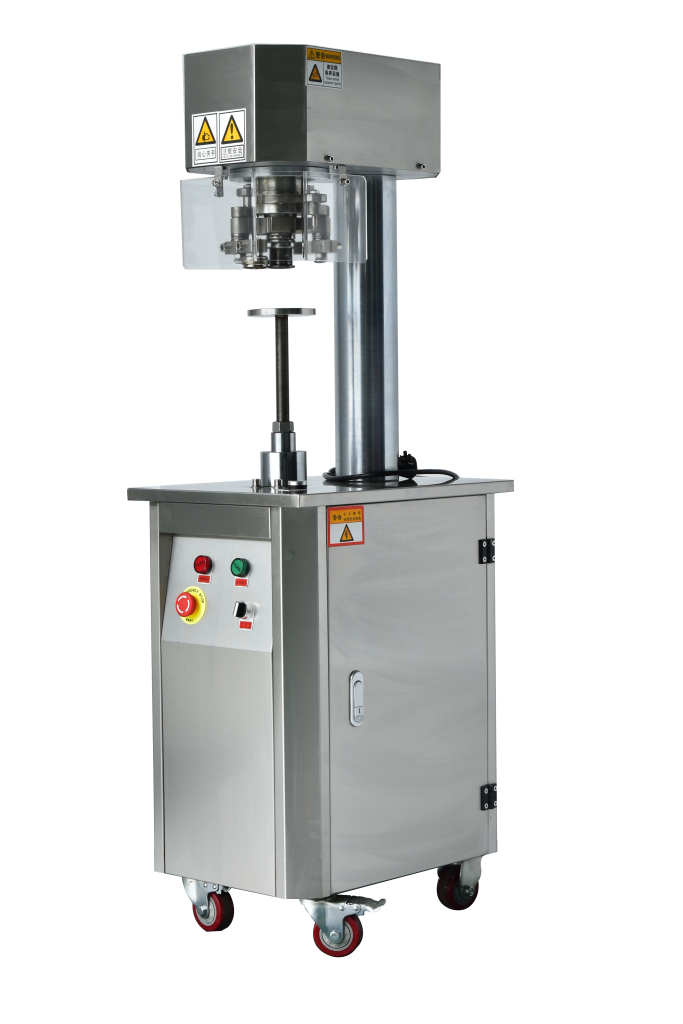
They also consume less energy and have lower maintenance costs. The simpler design and operation of semi-automatic can seamers mean fewer parts to replace and less complex servicing requirements.
Furthermore, the efficiency of semi-automatic can seamers leads to less waste. Accurate seaming reduces the number of defective cans, saving on materials and production costs.
The reduced need for extensive operator training also cuts costs. Operators can quickly become proficient in using the machine, minimizing the time and resources spent on training.
Overall, the combination of increased productivity, lower upfront and operational costs, and reduced waste makes semi-automatic can seamers an effective solution for saving time and reducing costs in the packaging process.