Dual-head servo can seamers bring about a significant improvement in both efficiency and precision through several key mechanisms.
In terms of efficiency, the presence of two seaming heads working concurrently is a major factor. This allows for a doubling of the sealing output within the same time frame compared to single-head machines. The parallel operation reduces the overall processing time for each can, enabling higher production volumes in a shorter period.
The servo technology incorporated in these seamers plays a crucial role in enhancing precision. It offers precise control over parameters such as pressure, speed, and position. This ensures that each can is sealed with consistent and accurate force, resulting in uniform and reliable seams.
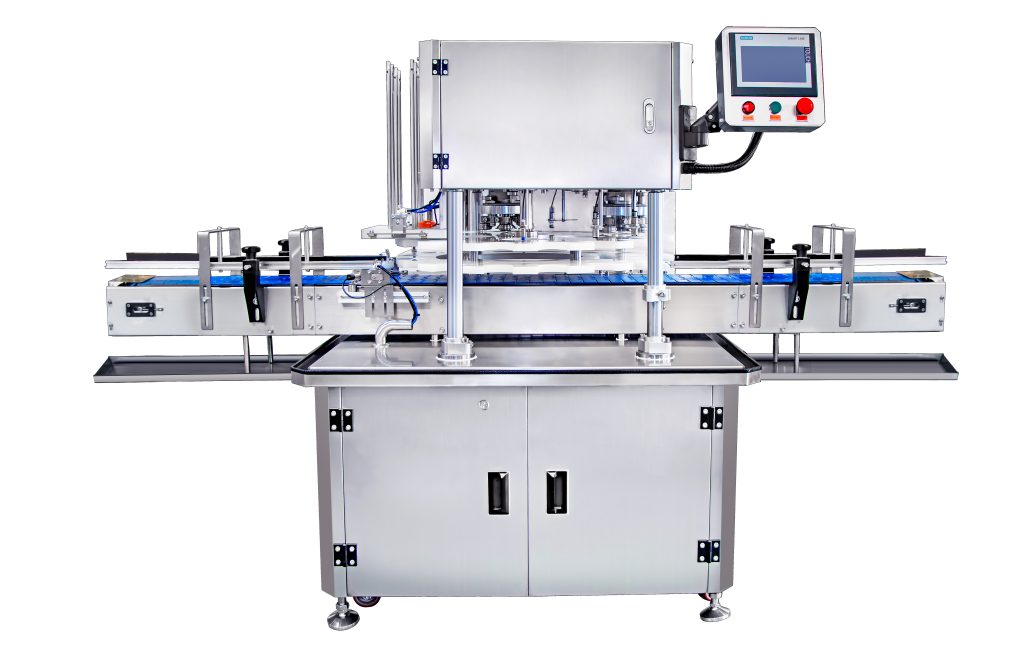
The advanced control systems of dual-head servo seamers enable real-time monitoring and adjustment of the seaming process. Any deviations or variations can be detected and corrected instantly, minimizing the chances of errors and ensuring that every seam meets the desired quality standards.
The seamless integration of mechanical and electronic components in these machines ensures smooth and uninterrupted operation. This reduces downtime due to mechanical failures or misalignments, further contributing to increased efficiency.
The ability to handle a wide range of can sizes and shapes with ease also adds to the efficiency. Without the need for frequent setup changes or adjustments, the seaming process can continue smoothly, minimizing production delays.
In summary, the combination of dual seaming heads and advanced servo technology in dual-head servo can seamers leads to a substantial improvement in efficiency and precision, making them indispensable in modern packaging operations.